湛江市發電站2號汽輪發電機的1號髙壓調節閥門打開失效,嚴重危害發電機組安全穩定運作。對閥體開展瓦解查驗,發覺髙壓變速氣門高壓閘閥下移10 mm,造成閥碟導向性凸肩擺脫導向槽,沒法對蒸氣開展正常的調整。由于發電機組臨修時間較短,高壓閘閥下移當場難以修復,確定選用噴焊解決,提升導向性凸肩的相對高度,做到修復髙壓主汽調節閥門原來的使用功能。
1 髙壓主汽調節閥門修補計劃方案
1.1 閥碟導向性凸肩工作中原理
2號發電機組為東方汽輪機廠生產制造的(N300-16.7/537/537-3型)汽輪發電機,它髙壓主汽調節閥門是通過1個主汽閥和2個調節閥門構成,髙壓調節閥門是用來調整高壓缸的進汽量。發電機組運行中,油動機做為機械設備提升機,使閥碟導向性凸肩沿導向槽左右挪動,操縱調節閥門碟的開啟度。發電機組運行中,調節閥門的高溫蒸汽為16.7 MPa,537℃,導向性凸肩關鍵承擔內應力和一定的軸向剪應力功效。
1號髙壓調節閥門的閥碟與高壓閘閥相互配合孔徑為170 mm,其閥碟的構造如下圖1所顯示,導向性凸肩規格為55 mm×30 mm×10 mm(高×寬×厚)。閥碟原材料選用20Cr3MoWVA碳素鋼,為了提高閥碟耐氣蝕的特性,其外表開展過持續高溫滲氮處理。
1.2 噴焊原材料和自動焊接設備的挑選
依據調節閥門的工作條件,閥碟導向性凸肩不僅確保有充足持續高溫抗壓強度,還得達到一定的耐磨性能。由于發電機組維修,不能購置到較佳配對原材料,參考噴焊原材料的選擇標準及其對各噴焊物理性能的剖析,采用與原材質材料相仿的TIG-R34(12Cr2MoWVTIB,Φ2.5 mm)焊條。自動焊接設備選用
Lincoln V300-1及氬弧焊接配套設施專用工具;溫度檢測應用國外MX2紅外測溫儀。
2 焊接性能剖析
依據碳當量計算公式,原材料20Cr3MoWVA的主要特點是含碳量及合金元素比較多,電焊焊接時焊接及熱處理工藝區非常容易發生淬硬機構,當焊接件剛度及連接頭地應力比較大時,非常容易造成冷裂紋。
通過滲氮處理的閥碟,其表面硬度達到HV900,電焊焊接時非常容易產生裂紋。
3 噴焊加工工藝
3.1 工藝路線
焊前打磨拋光清理-加熱-噴焊-焊后熱處理-焊后銑削。
3.2 焊前提前準備
最先用角向砂輪打磨完全清除除去噴焊位置20 mm范疇里的高頻淬火層,打磨拋光深層應超過0.4 mm,精確測量打磨拋光位置的硬度值,并確保焊接地區做到HB185~321的規定。按JB4730-94測試標準,查驗打磨拋光前的導向性凸肩表層質量不可有裂痕、焊瘤等缺點,做到Ⅰ級規范為達標。
然后用甲苯清理閥碟電焊焊接位置以及周邊50 mm范圍之內,確保沒有水、油等;用打磨砂紙消除氬弧焊絲表層的油漬和銹點等臟污。
3.3 焊接方法及主要參數
選用氧乙炔火苗加溫的辦法開展焊前加熱,加熱環境溫度為350~400℃,用紅外測溫儀精確測量加熱環境溫度。閥碟電焊焊接位置外露,其余部件用石棉布覆蓋,防止電弧燒傷。工藝參數I=80~90 A,氬氣瓶總流量8~10L/min,直流電正接,電壓范圍10~15 V,焊接速度30~45 mm/min,每道晃動總寬≤10 mm,每層噴焊薄厚≤4 mm。加熱環境溫度做到后進行電焊,固層溫控在300~400℃,焊接過程中不容許造成一切缺點,關鍵查驗引、收弧處,發覺缺點馬上用角向磨光機除去。為確保加工的剩余量,按圖噴焊規格,直徑提升5 mm,公稱直徑降低5 mm,堆碼13 mm。一邊噴焊結束后再噴焊另一邊。
電焊焊接結束后,用硅酸鋁纖維氈防火棉覆蓋緩冷,電焊焊接位置凍到100~150℃,馬上開展焊后部分熱處理工藝。熱處理工藝選用火苗加溫至640~660℃,隔熱保溫30 min,用紅外測溫儀檢測,升溫速度和冷卻速度均<300℃/h,制冷至300℃下列并不操縱,制冷時要硅酸鋁纖維毯覆蓋緩冷。
4 焊后檢測
依照工藝路線進行閥碟的噴焊和機械加工制造后,經滲透探傷和超聲探傷儀查驗,焊接并沒有裂痕、焊瘤、孔洞等缺點品質,噴焊品質做到JB4730-94規范Ⅰ級的規定;在生產表層開展硬度標準,其均值硬度值為HB241,與原原材質的硬度值相仿,滿足需要產品工件的性能指標。
5 結 論
2號發電機組1號髙壓主汽調節閥門電焊焊接修補并運作近1年之后,在發電機組維修時瓦解查驗,噴焊的閥碟凸肩經5 616 h運作未發現任何問題。由此可見用TIG-R34氬弧焊絲噴焊20Cr3MoWVA原材料選用加熱350~400℃,焊后640~650℃,隔熱保溫30 min解決的焊接方法是有效可行的。它不僅解決了髙壓主汽調節閥門正常的對蒸氣開展調整,還節約了幾萬元財力。
1 髙壓主汽調節閥門修補計劃方案
1.1 閥碟導向性凸肩工作中原理
2號發電機組為東方汽輪機廠生產制造的(N300-16.7/537/537-3型)汽輪發電機,它髙壓主汽調節閥門是通過1個主汽閥和2個調節閥門構成,髙壓調節閥門是用來調整高壓缸的進汽量。發電機組運行中,油動機做為機械設備提升機,使閥碟導向性凸肩沿導向槽左右挪動,操縱調節閥門碟的開啟度。發電機組運行中,調節閥門的高溫蒸汽為16.7 MPa,537℃,導向性凸肩關鍵承擔內應力和一定的軸向剪應力功效。
1號髙壓調節閥門的閥碟與高壓閘閥相互配合孔徑為170 mm,其閥碟的構造如下圖1所顯示,導向性凸肩規格為55 mm×30 mm×10 mm(高×寬×厚)。閥碟原材料選用20Cr3MoWVA碳素鋼,為了提高閥碟耐氣蝕的特性,其外表開展過持續高溫滲氮處理。
1.2 噴焊原材料和自動焊接設備的挑選
依據調節閥門的工作條件,閥碟導向性凸肩不僅確保有充足持續高溫抗壓強度,還得達到一定的耐磨性能。由于發電機組維修,不能購置到較佳配對原材料,參考噴焊原材料的選擇標準及其對各噴焊物理性能的剖析,采用與原材質材料相仿的TIG-R34(12Cr2MoWVTIB,Φ2.5 mm)焊條。自動焊接設備選用
Lincoln V300-1及氬弧焊接配套設施專用工具;溫度檢測應用國外MX2紅外測溫儀。
2 焊接性能剖析
依據碳當量計算公式,原材料20Cr3MoWVA的主要特點是含碳量及合金元素比較多,電焊焊接時焊接及熱處理工藝區非常容易發生淬硬機構,當焊接件剛度及連接頭地應力比較大時,非常容易造成冷裂紋。
通過滲氮處理的閥碟,其表面硬度達到HV900,電焊焊接時非常容易產生裂紋。
3 噴焊加工工藝
3.1 工藝路線
焊前打磨拋光清理-加熱-噴焊-焊后熱處理-焊后銑削。
3.2 焊前提前準備
最先用角向砂輪打磨完全清除除去噴焊位置20 mm范疇里的高頻淬火層,打磨拋光深層應超過0.4 mm,精確測量打磨拋光位置的硬度值,并確保焊接地區做到HB185~321的規定。按JB4730-94測試標準,查驗打磨拋光前的導向性凸肩表層質量不可有裂痕、焊瘤等缺點,做到Ⅰ級規范為達標。
然后用甲苯清理閥碟電焊焊接位置以及周邊50 mm范圍之內,確保沒有水、油等;用打磨砂紙消除氬弧焊絲表層的油漬和銹點等臟污。
3.3 焊接方法及主要參數
選用氧乙炔火苗加溫的辦法開展焊前加熱,加熱環境溫度為350~400℃,用紅外測溫儀精確測量加熱環境溫度。閥碟電焊焊接位置外露,其余部件用石棉布覆蓋,防止電弧燒傷。工藝參數I=80~90 A,氬氣瓶總流量8~10L/min,直流電正接,電壓范圍10~15 V,焊接速度30~45 mm/min,每道晃動總寬≤10 mm,每層噴焊薄厚≤4 mm。加熱環境溫度做到后進行電焊,固層溫控在300~400℃,焊接過程中不容許造成一切缺點,關鍵查驗引、收弧處,發覺缺點馬上用角向磨光機除去。為確保加工的剩余量,按圖噴焊規格,直徑提升5 mm,公稱直徑降低5 mm,堆碼13 mm。一邊噴焊結束后再噴焊另一邊。
電焊焊接結束后,用硅酸鋁纖維氈防火棉覆蓋緩冷,電焊焊接位置凍到100~150℃,馬上開展焊后部分熱處理工藝。熱處理工藝選用火苗加溫至640~660℃,隔熱保溫30 min,用紅外測溫儀檢測,升溫速度和冷卻速度均<300℃/h,制冷至300℃下列并不操縱,制冷時要硅酸鋁纖維毯覆蓋緩冷。
4 焊后檢測
依照工藝路線進行閥碟的噴焊和機械加工制造后,經滲透探傷和超聲探傷儀查驗,焊接并沒有裂痕、焊瘤、孔洞等缺點品質,噴焊品質做到JB4730-94規范Ⅰ級的規定;在生產表層開展硬度標準,其均值硬度值為HB241,與原原材質的硬度值相仿,滿足需要產品工件的性能指標。
5 結 論
2號發電機組1號髙壓主汽調節閥門電焊焊接修補并運作近1年之后,在發電機組維修時瓦解查驗,噴焊的閥碟凸肩經5 616 h運作未發現任何問題。由此可見用TIG-R34氬弧焊絲噴焊20Cr3MoWVA原材料選用加熱350~400℃,焊后640~650℃,隔熱保溫30 min解決的焊接方法是有效可行的。它不僅解決了髙壓主汽調節閥門正常的對蒸氣開展調整,還節約了幾萬元財力。
上一篇多用途水泵控制閥的作用特點
下一篇抗腐蝕調節閥選型提醒
咨詢需求
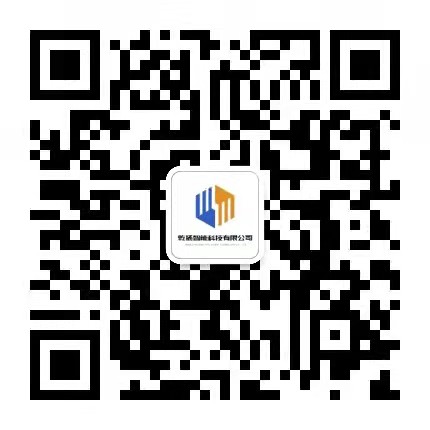